Le esperienze delle aziende italiane nel campo della produzione data-driven stanno raggiungendo un buon livello di maturità. Ma la smart factory ha bisogno di tante cose: obiettivi chiari, gestione del cambiamento e una vista unificata sulle informazioni. Con la partecipazione di Artsana, Barilla, Bianchi Bicycles, Orange Business, Pellini e Qlik
Il traguardo della fabbrica smart è da molti anni al centro di molte forme di promozione culturale e incentivazione, più o meno diretta, sia finanziaria sia fiscale. Le basi teoriche della trasformazione digitale del settore manifatturiero sono chiare e condivisibili: rispetto a un passato in cui dominavano certe doti qualitative – il “bernoccolo” dell’imprenditore, l’intuito e la competenza del direttore di produzione, la maestria tecnica e la manualità dei singoli operatori – la maggiore attenzione ad aspetti quantitativi più misurabili – come processi, tempistiche, qualità del prodotto, ma soprattutto più contestualizzati nel complesso sistema di relazioni e condizioni al contorno che lega i prodotti al mercato dei loro clienti finali – non può che portare a una maggiore capacità di governo. Se lo scopo è arrivare alla fabbrica più agile nel gestire impianti, approvvigionamenti, logistica, costi di energia e materie prime, strumenti come l’IoT e il data analytics diventano quasi naturali. Il problema, più che tecnico, è legato alla cultura, alla preparazione delle persone, alla propensione a reimpostare modalità di lavoro consolidatesi molto prima che la convergenza tra IT e Operation technologies rendesse possibili certe opportunità. Inoltre, la fabbrica ha mille motivi per resistere agli slogan troppo facili: in un contesto dove la continuità produttiva è spesso l’obiettivo principale, la digitalizzazione e l’automazione non possono essere calate dall’alto, ma devono essere ben calibrate e metabolizzate. Magari partendo da una digitalizzazione di sistema, in grado di alimentare competenze e scelte Industry 4.0 fin dai banchi delle scuole professionali e dall’università. Con la partecipazione di Artsana, Barilla, Bianchi Bicycles, Orange Business, Pellini e Qlik, la tavola rotonda di Data Manager dedicata all’intelligent industry si focalizza proprio sugli aspetti delle competenze e del change management, facendo leva sul confronto dei progetti di smart industry più avanzati per distillare una possibile ricetta di trasformazione applicabile anche in contesti aziendali di dimensioni meno estese, o in ambiti applicativi più ristretti. Alla ricerca di una scalabilità, che vada oltre le fasi della sperimentazione e dei proof of concept.
PROGETTUALITÀ IN CORSO
Come di consueto, la regia intorno al tavolo ha previsto due giri di interventi. Il primo dedicato al racconto e al confronto di esperienze e progetti di smart factory in corso d’opera nelle rispettive realtà aziendali, con particolare riferimento agli obiettivi della digitalizzazione, alle scelte tecnologiche e agli aspetti dell’organizzazione e della governance, come la creazione di nuove figure di leadership e coordinamento, la relazione con le altre funzioni di management, l’eterna questione della formazione non solo tecnica delle persone e la gestione del cambiamento rispetto a procedure acquisite e abitudini radicate.
Nella seconda parte della discussione, i partecipanti hanno preso in esame le principali aree di criticità, tanto quelle riscontrate a livello di implementazione e corretta adozione delle soluzioni individuate quanto quelle che l’introduzione di soluzioni di nuova generazione come le tecnologie connesse finiscono inevitabilmente per comportare, focalizzando l’attenzione sull’intreccio tra sicurezza fisica, logica dei dati e fattore umano, compliance normativa degli ambienti di produzione, impatto ambientale e sostenibilità energetica. Anche un’azienda di forte tradizione come Barilla, in un comparto che si ispira molto alla manualità e all’artigianalità delle lavorazioni, oggi riconosce il bisogno di automatizzare e di evolvere tecnologicamente. Lo ricorda, in apertura di tavola rotonda Gianpaolo Vitulano, Global data architecture & governance, AA & AI sr manager di Barilla Group. «Uno degli obiettivi è avere sempre maggior controllo e massima visibilità sulle produzioni, la qualità, la gestione della fabbrica e dell’azienda in generale». Nel 2020 Barilla, aveva già attuato diversi progetti di automazione estesa nei suoi stabilimenti. «Con l’avvio poi dell’attuale programma di digitalizzazione – spiega Vitulano – abbiamo voluto cogliere l’opportunità per centralizzare il patrimonio digitale e renderlo più accessibile e quindi utilizzabile a tutti i livelli e dipartimenti in azienda. Insomma, l’obiettivo è una comunione di informazioni digitali molto trasversali in grado di tradursi in capacità di controllo». Si tratta di uno sforzo che oggi – a giudizio di Vitulano – molte aziende del calibro di Barilla stanno compiendo e devono compiere per rimanere competitive sul mercato. Tra i tanti progetti, alcuni costituiscono un’evoluzione delle pratiche di controllo della qualità, non limitato solo al singolo prodotto, ma anche, per esempio, alla gestione di materiali per l’imballaggio. L’obiettivo è, in quel caso, implementare nei vari stabilimenti, un processo di confezionamento ottimizzato in base alle scorte disponibili in loco. Altri progetti possono mirare a migliorare gli aspetti logistici. «In un contesto di mercato sempre più sensibile a tali tematiche, ci si può occupare, per esempio, dell’automazione della gestione degli allergeni, approfondendo la comprensione dei tipi di ingredienti associati ai diversi siti produttivi, esplorando la possibilità di sostituzione e determinare le informazioni specifiche da includere nella fase di etichettatura».
Ma la fabbrica intelligente è anche un organismo che può essere seguito in modo molto più proficuo sul piano del funzionamento e dell’usura degli impianti. «Barilla ha implementato soluzioni che consentono di mitigare il rischio di potenziali malfunzionamenti e di evitare costosi down-time» – precisa il responsabile delle architetture dati. «Un aspetto importante di questo lavoro comporta anche momenti di formazione in cui non si parla semplicemente delle nuove tecnologie di automazione, ma si cerca di mostrare come il dato digitale possa integrarsi in tutte le attività quotidiane, coinvolgendo ogni livello gerarchico». La funzione di Vitulano affronta anche la questione degli strumenti analitici avanzati che stanno trasformando e allargando molto la base d’uso della business intelligence. «La sicurezza informatica è una delle nostre massime priorità, specialmente considerando che in passato i nostri impianti funzionavano come vere e proprie entità isolate. Attualmente, dobbiamo capire come integrarli e garantire la loro protezione costante, attraverso l’utilizzo di sistemi di segregazione logica per reti e informazioni».
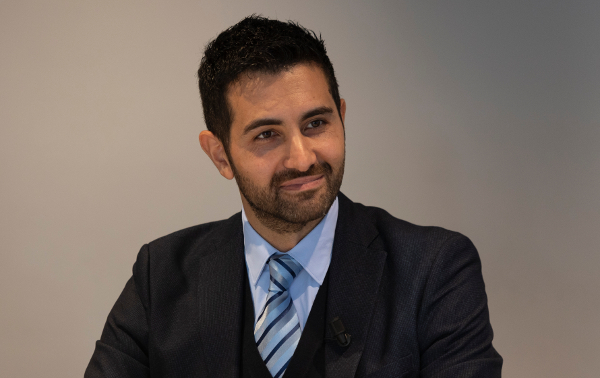
RIMONTARE LA BICICLETTA
Di senso opposto e ispirata al principio della “tabula rasa” la strategia di trasformazione digitale adottata da Bianchi Bicycles per trasformare in senso digitale la produzione delle biciclette – un prodotto che oggi vede la distinzione tra il tradizionale segmento delle “muscolari” e i modelli a trazione elettricamente assistita. L’azienda – come racconta il CIO Mauro Toso – ha vissuto un primo momento di “migrazione culturale” del personale di fabbrica proprio per favorire e affinare la capacità di raccogliere e seguire il dato digitale. «Abbiamo quindi deciso che anziché apportare modifiche a una linea già esistente, sarebbe stato più opportuno concepire un nuovo stabilimento. Il nuovo impianto non solo si autoalimenta dal punto di vista energetico, ma è anche provvisto di pannelli solari e sistemi di recupero energetico dal sottosuolo, garantendo così climatizzazione sia in estate che in inverno».
È nata così un’officina delle biciclette davvero avveniristica e innovativa, un esempio per l’intero settore. «Anche dal punto di vista operativo abbiamo radicalmente cambiato la logica dell’assemblaggio» – spiega Toso. «La bicicletta da assemblare si sposta da una postazione all’altra su una slitta bilanciata, fornita di tutti le componenti e gli strumenti necessari». Nella nuova smart factory Bianchi si registra la presenza di ben 2.500 punti rete e altri accorgimenti che hanno rappresentato una sfida tecnologica e impiantistica anche in termini di cybersecurity. «Perché dove porti sensoristica connessa – spiega Toso – porti implicitamente delle potenziali vulnerabilità». Analoghe difficoltà ha comportato la realizzazione del magazzino materiali, adattato all’esigenza di predisporre i kit di montaggio associati alla bicicletta che viene assemblata. Il risultato finale vede un totale di un centinaio di postazioni di lavoro, ciascuna asservita al software di fabbrica e dotata di schermi che assistono il personale nelle fasi di preparazione. Ciascuna postazione è connessa all’interno di una architettura SCADA che per Bianchi rappresenta un grande salto trasformativo. «Si tratta di un territorio completamente nuovo, ammette Toso, poiché il punto di partenza era una fabbrica con pochi terminali di raccolta dati. Oggi, invece, gestiamo cento postazioni con i loro schermi touch, e ciò che un tempo richiedeva l’inserimento manuale dei dati avviene ora in modo automatico grazie ai sensori». Oltre alla sfida tecnologica, Bianchi ha affrontato una significativa sfida culturale sin dalla concezione del nuovo stabilimento e dei suoi processi. «Abbiamo investito molto sulla risorsa umana, individuando i responsabili dei singoli progetti trasformativi in modo che fossero tutti molto focalizzati sugli aspetti business. Il mio team IT è stato il facilitatore tecnologico di un piano la cui esecuzione avveniva nel business, dentro ai suoi processi, integrando il magazzino, la logistica, il team di fabbrica, l’industrializzazione del prodotto, il sistema SCADA, il software MES e altri aspetti. Per ciascuna voce sono stati individuati dei ruoli di responsabilità chiamati a dare un contributo legato alle “vere” necessità del lavoro di ideazione e assemblaggio di una bicicletta e questa è stata sicuramente una chiave importante di successo».
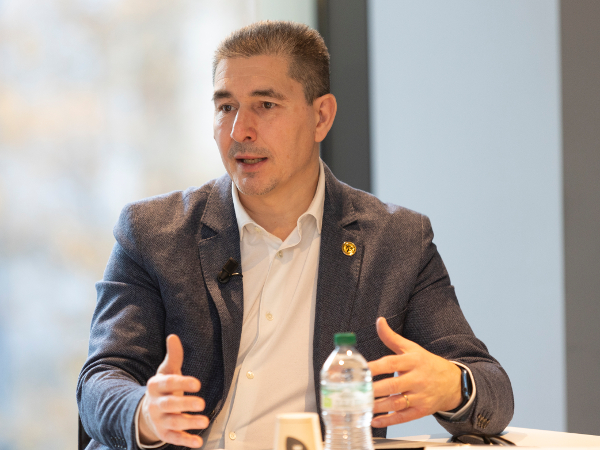
STRUMENTI PER CONOSCERE
Secondo Giorgio Dossena, presales manager di Qlik, azienda leader nell’integrazione e nella governance dei dati che offre soluzioni complete che funzionano con fonti di dati differenti, i casi appena esposti da Barilla e Bianchi Bicycles dimostrano che in questi progetti di trasformazione la tecnologia deve essere considerata un mezzo a supporto, non un fine. L’obiettivo vero è rispondere a esigenze di business attraverso un cambiamento che bisogna gestire in modo adeguato. «Intendo dire che in Bianchi quei 2500 punti rete non sono una scelta casuale» – spiega Dossena. «Quelle connessioni sono al servizio di specifici use case: per esempio la possibilità di acquisire tramite barcode un dato che mi servirà anche in seguito, nel post vendita. Dall’altro lato, Barilla sfrutta la tecnologia per una gestione ottimizzata delle informazioni, inclusa la rilevazione rapida di ingredienti allergenici, già presenti in passato, ma ora raccolti in modo più tempestivo. Ciò contribuisce a rendere l’azienda ancora più competitiva».
La mission di Qlik è di trasformare ambienti di dati complessi in informazioni fruibili, ovvero mettere a disposizione delle aziende manifatturiere strumenti che a valle delle tecnologie della fabbrica intelligente – sensori, lettori, reti cablate e wireless, IoT – servono per governare l’enorme mole di dati che in questo modo viene raccolta, concentrata e nuovamente distribuita. «Oggi – avverte Dossena – questi dati rendono possibili un business sempre più real-time». Un concetto molto diverso da quella che era la “produzione real-time” che molte fabbriche hanno adottato: un modo per gestire lo sviluppo e la creazione di un prodotto in parallelo alle attività di vendita, marketing e promozione, assistenza al cliente. La tecnologia Qlik si rivolge a chi deve assicurare coerenza e qualità dei dati; agli esperti che realizzano data warehouse e applicazioni statistiche; a chi deve tradurre il dato in informazioni facilmente fruibili, sulle quali prendere molto in fretta delle decisioni consapevoli. «La tecnologia da sola non basta per rendere vincente un progetto di trasformazione» – continua Dossena. «Ecco perché recentemente Qlik si è focalizzata molto sulla data literacy, ovvero sull’alfabetizzazione del dato, con un’offerta che mira ad aiutare le aziende a utilizzare meglio i loro dati, a presentarli e leggerli in maniera più efficace. In una parola, a dare valore al dato». Nella lunga esperienza di Dossena, i modelli di fabbrica digitale di maggior successo sono quelli che riescono a trovare il giusto connubio tra il potenziale della tecnologia e le ragioni di business: la marginalità, la velocità, la competitività, la soddisfazione del cliente, l’impatto ambientale e sociale.
E Gianpaolo Vitulano di Barilla, si dice molto d’accordo. «Nel lavoro sui dati, nella loro integrazione, ci sono costi che vanno giustificati. Occorre dare un senso a questo lavoro, creando un catalogo ragionato delle informazioni che ci servono. Lo si fa in base alle necessità progettuali di una pianificazione in cui Business e IT collaborano strettamente. L’informazione digitale diventa un “prodotto” che devo costruire e vendere». L’alfabetizzazione contribuisce anche alla riduzione di un altro grande rischio: quello di duplicare e/o accumulare quantità eccessive di “materia prima” informativa. Dati costosi da acquisire e governare che si rivelano poi magari anche a basso rendimento. La cultura del dato nella fabbrica deve servire proprio a creare una diffusa consapevolezza dell’utilità e del valore delle informazioni che vengono raccolte e condivise internamente. Qlik ha sviluppato un sistema di strumenti di valutazione, affiancati da moduli di e-learning che abilitano questa consapevolezza, potenziando le attività di formazione con tecnologie di machine learning che rendono i suoi strumenti più semplici e user friendly, grazie per esempio ad automatismi per la raccolta e l’integrazione, suggerimenti per la realizzazione di grafici più significativi. E facilitando al tempo stesso quel concetto di “fiducia” nel dato che è alla base della fabbrica data driven.
È importante lavorare molto nella direzione dell’autorevolezza dell’informazione. «Quando mi confronto con altre realtà industriali – spiega Vitulano – mi rendo conto dell’importanza che oggi ha il cambio generazionale all’interno delle grandi organizzazioni. Noi tutti veniamo da un’epoca e da aziende in cui l’intuito, la “pancia” contava moltissimo. Oggi, sappiamo che a volte i dati possono smentire l’intuito. Ma l’impulso verso questa consapevolezza deve venire dall’alto per essere davvero trasformativo e deve basarsi sulla fiducia». Per questo uno dei compiti della funzione di Vitulano in Barilla è realizzare quei processi di certificazione del dato che si traducono in veridicità e attendibilità delle informazioni prodotte, quando si tratta di decidere sulla base di quelle informazioni o di formulare nuove domande, inventando così nuovi use case.

Per Roberto Bresciano, industrial director di Artsana Group, l’intelligenza nella produzione diventa una formidabile arma per gestire la complessità di un mercato in continua evoluzione, e oltretutto condizionato dal rispetto di normative sui prodotti e di stili di consumo estremamente diversificati. Il grande gruppo lombardo annovera una vasta gamma di prodotti che spaziano dalla cosmetica ai giochi per la prima infanzia, fino all’abbigliamento e agli accessori, carrozzine e seggiolini per auto. «Operando in un contesto internazionale, ci troviamo ad affrontare una varietà di normative molto diverse, e soddisfare tutte le parti coinvolte rappresenta una sfida estremamente complessa» – spiega Bresciano. Artsana ha vissuto in prima linea la fase di modernizzazione mirata all’efficientamento e alla produttività e oggi prosegue sulla strada del cambiamento, operando su due direzioni diverse ma, allo stesso tempo, correlate: da un lato la produttività in senso “classico”, giocata sulla continua ottimizzazione delle linee produttive, dall’altro l’ottimizzazione dei consumi energetici.
«In entrambi gli ambiti – continua l’industrial director di Artsana – la digitalizzazione sta entrando prepotentemente nella nostra operatività. Sul lato produttivo, ad esempio, grazie al grande gioco di squadra tra IT e produzione, sono stati implementati nuovi sistemi MES nei vari impianti». Guardando alle esperienze dei colleghi, Roberto Bresciano rileva due peculiarità importanti: «Non solo il digitale trasforma profondamente gli stessi processi di fabbrica, ma contribuisce a creare un contesto decisionale e di responsabilità molto più esteso». L’adozione di un ambiente MES moderno, ha dato ad Artsana l’opportunità di arricchire il patrimonio informativo della fabbrica e di favorire una maggiore democrazia del dato che oggi viene distribuito a un insieme sempre più vasto di funzioni. «Se limito la distribuzione delle informazioni solo al responsabile di linea o al direttore dello stabilimento, c’è il rischio che gli altri componenti del team non si sentano coinvolti nel processo. Per evitarlo, abbiamo implementato un sistema in cui ogni individuo riceve i dati necessari per valutare le prestazioni nelle mansioni specifiche e risolvere le questioni rilevanti, ciascuno al proprio livello di pertinenza. Naturalmente, è prevista una procedura di escalation per le problematiche di maggiore portata, ma il sistema MES di Artsana è progettato per consentire diversi livelli di utilizzo». «Questa distribuzione più ampia delle informazioni – sottolinea Bresciano – ha avuto un impatto positivo sulla reportistica e sulle interfacce con il sistema MES installato nelle diverse postazioni di lavoro. Ogni addetto è ora in grado di visualizzare le informazioni relative al proprio contributo alla produzione e di utilizzarle come punto di riferimento».
Un analogo sforzo di quantificazione è stato fatto sulle tematiche energetiche, attraverso un sistema di metering molto capillare dove Artsana replica le capacità di approfondimento del MES, disseminando i dati relativi all’energia consumata. Questa capillarità riguarda anche l’impiego stesso dell’energia. «Nell’impianto in Romania dove Artsana produce i suoi materiali tessili, la produzione è organizzata per moduli di circa 30 persone, ciascuna dotata di macchine cucitrici» – spiega Bresciano. Oltre alle luci di fabbrica, ogni postazione ha una sua luce individuale e proprio grazie ai dati relativi ai consumi sono arrivati anche suggerimenti di azioni di risparmio. Alle luci è stato per esempio aggiunto un interruttore che permette di spegnere la lampada individuale quando l’operatore esce per la pausa pranzo». A questo esempio potrebbero aggiungersene tanti altri: Artsana, sostiene l’industrial director, sta correndo una serie di sprint paralleli, non una sola maratona.
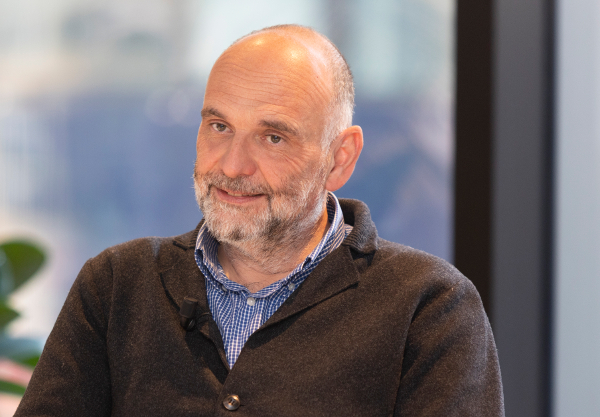
SCHERMATURE SULLO SCHERMO
Dopo la storia di un grande produttore di beni di consumo con quasi diecimila dipendenti e un catalogo ampio e diversificato ecco il caso, anch’esso lombardo, della Pellini di Codogno in provincia di Lodi. Una media azienda che impiega trecento persone in Italia e in Repubblica Ceca e che, nei suoi cinquant’anni di storia, ha raggiunto una posizione riconosciuta su scala mondiale con una produzione molto specializzata, le schermature solari, alcune delle quali trovano applicazione in avveniristici edifici a sviluppo verticale, tra cui le tre Torri di CityLife a Milano. «Già negli anni ‘90 – racconta il responsabile IT Fabio Pericotti, Pellini getta le basi del suo prodotto distintivo, la “tenda nel vetro”, un segmento in cui siamo leader internazionali. Si tratta di sistemi schermanti che vengono direttamente inseriti all’interno della vetrata isolante». Nel corso del tempo, Pellini ha aggiunto altri segmenti, ottenendo un particolare successo nel settore nautico, con le sue soluzioni custom destinate all’arredo degli yacht di lusso. «Le prime fasi della nostra modernizzazione si sono attuate con l’adattamento dei macchinari al successivo passo di digitalizzazione» – spiega Pericotti. «In queste fasi si possono riconoscere due tipologie di progetto. Una di tipo “push”, come la stessa adozione di sistemi di produzione dotati di interfacce di interconnessione, o l’integrazione dei nostri magazzini verticali al sistema MES che è in funzione da diversi anni e ci ha permesso di accumulare già una serie di dati storici da utilizzare in futuro. L’altro più di tipo “pull”, in cui cerchiamo di far leva sulle tecnologie adottate per raggiungere obiettivi specifici». Per esempio, un progetto importante riguarda la completa dematerializzazione di processi produttivi che impiegano ancora molte informazioni su supporto cartaceo. «Vogliamo far circolare queste informazioni in modo completamente diverso, meno statico, per rispondere alle esigenze di una produzione che avviene su commessa». Nella specificità della trasformazione digitale di Pellini c’è anche un filone di natura strettamente tecnologica che l’azienda sta vivendo non come consumatore, bensì come produttore. «Uno dei progetti in corso riguarda la realizzazione in proprio dell’elettronica di controllo che va all’interno delle nostre sofisticate tende nel vetro» – continua Pericotti. «L’obiettivo è portare interamente in-house la costruzione di queste schede elettroniche, acquisendo in prima persona un know-how di cui Pellini inizialmente non disponeva. Per farlo, abbiamo costituito un team di una quindicina di persone seguite da consulenti che ci hanno aiutato a strutturare la progettazione di questi sistemi di controllo, dandoci un certo vantaggio sul piano della comprensione delle tecnologie più all’avanguardia. Abbiamo puntato molto sulla formazione di nuove competenze e sull’utilità di un approccio diverso che ci permette di andare oltre i limiti del conosciuto, perseguendo nuovi obiettivi in modo più strutturato» – conclude il responsabile IT di Pellini.
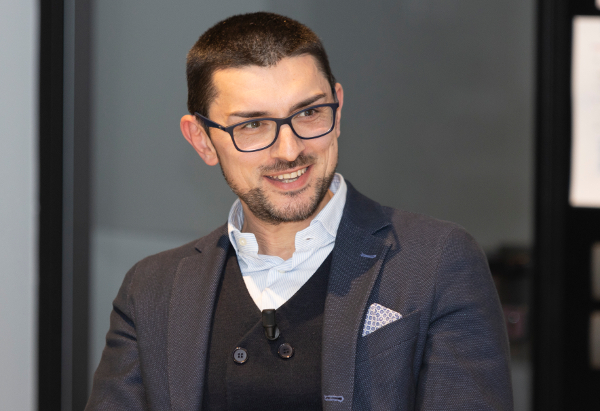
In base alle testimonianze sinora condivise, emergono chiaramente – come evidenzia Pier Giuseppe Dal Farra, smart industries business expert di Orange Business – due aspetti predominanti. «In primo luogo, la necessità di un empowerment, cioè di estendere la trasformazione coinvolgendo il maggior numero possibile di individui. Il secondo aspetto, strettamente connesso al primo, riguarda la capacità di gestire il cambiamento, partendo dalle concrete esigenze di business, anziché limitarsi alla disponibilità di tecnologia». In questo contesto, Orange Business, con i suoi 27mila esperti distribuiti in tutto il mondo e con squadre specializzate in tematiche specifiche come big data, smart industries, intelligenza artificiale e sicurezza informatica, presenta una proposta articolata su quattro aree d’intervento. «La mia area, focalizzata sulla fabbrica intelligente, si affianca ad altre aree di evoluzione come cloud e sicurezza, smart working e customer experience, con l’obiettivo di dimostrare concretamente come la trasformazione digitale possa contribuire all’evoluzione dell’intero settore produttivo».
MODELLI DA SCALARE
La fabbrica intelligente sta vivendo una trasformazione straordinaria, spinta da due forze trainanti di rilevanza cruciale. Da un lato, l’urgenza della sostenibilità energetica, dettata dalle dinamiche climatiche e geopolitiche in corso. Dall’altro, una crescente attenzione alla sicurezza delle persone e alla riduzione del rischio di incidenti, particolarmente significativa nel contesto manufatturiero. Già si parla di Industry 5.0 per descrivere gli ambienti produttivi in cui l’interazione tra uomo e robot industriali avviene in modo ravvicinato. «Che si tratti della quarta o quinta rivoluzione industriale – continua Dal Farra – la sfida principale per tutti i nostri clienti è di integrare la tecnologia nella realtà della fabbrica in modo veramente scalabile. Le ricerche indicano che solo una minima percentuale di numerosi proof of concept e progetti riesce a superare la fase sperimentale». Due le cause principali: «Mancanza di una visione d’insieme e di obiettivi chiaramente definiti. Un ulteriore elemento critico riguarda l’engagement delle risorse umane nel contesto del processo di change management. La difficoltà risiede nella necessità di gestire in modo efficace la trasformazione, coinvolgendo e motivando il personale in un contesto di cambiamento. Un adeguato approccio al change management permette l’adozione diffusa di nuove dinamiche all’interno dell’organizzazione e può fare la differenza tra successo e fallimento».
La divisione Smart Industries di Orange Business, importante system integrator francese, dispone di un gruppo di professionisti che si occupa in modo specifico di change management, fornendo ai clienti una serie di strumenti concreti come i corsi di alfabetizzazione, lo studio degli indicatori da utilizzare per misurare i progressi fatti e un insieme di servizi dedicati alle risorse umane. Un caso concreto – illustrato da Dal Farra – riguarda la collaborazione con il gruppo aerospaziale Safran, tra i principali produttori mondiali di motori per aeromobili, che gestisce stabilimenti di grandi dimensioni, dove vengono utilizzati decine di migliaia di strumenti, dai singoli utensili ai mezzi mobili, come muletti e camioncini. In queste megafabbriche, Safran si trova ad affrontare l’oneroso problema della localizzazione, smarrimento o furto di strumentazione. «Il primo progetto di tracciamento di tutti questi oggetti ha determinato la riduzione significativa, quasi del 10%, del tempo richiesto per individuare gli attrezzi smarriti. In contesti di fabbriche così estese, tale margine si traduce in un notevole risparmio di costi. L’introduzione di dashboard e reportistica accurata sulla distribuzione degli attrezzi consente inoltre un’analisi approfondita dell’allocazione di tali strumenti ai vari utilizzatori. Questo non solo facilita approvvigionamenti più strategici, ma promuove anche una maggiore responsabilizzazione delle persone, incoraggiandole a una gestione più attenta delle attrezzature utilizzate».
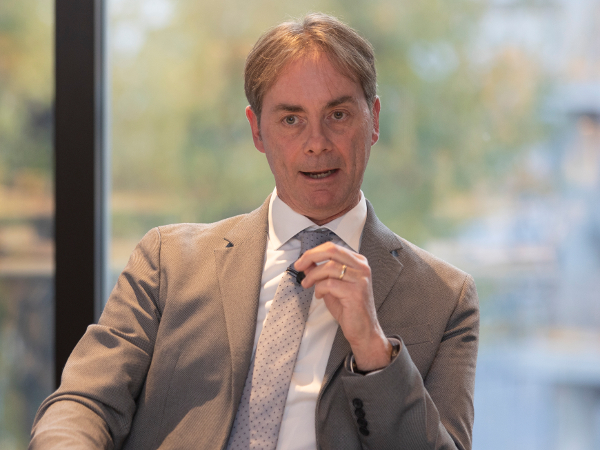
Nei progetti di trasformazione, si presentano numerose opportunità da sfruttare, ma, naturalmente, emergono anche sfide da affrontare. «Lato manutenzione, per esempio, – interviene ancora Vitulano di Barilla – mediante l’adozione di adeguate pratiche preventive, possiamo ottimizzare la gestione del ciclo di vita delle macchine e, parallelamente, elevare il livello di sicurezza degli operatori. La realtà virtuale ci aiuta nella gestione anche a distanza degli impianti». L’adozione della digitalizzazione comporta un incremento della superficie esposta al rischio di compromissione dei dati, implicando altresì nuovi obblighi di gestione e controllo dei processi automatizzati. «Proprio per questo – sottolinea Vitulano – qualsiasi azienda, che intraprende questo percorso, ha necessità di investire in cybersecurity. Sull’altro piano della bilancia, digitalizzare significa anche avere a disposizione informazioni che non servono soltanto al business, ma al rispetto dei numerosi vincoli normativi di settore».
L’adozione della digitalizzazione comporta un incremento della superficie esposta al rischio di compromissione dei dati, implicando altresì nuovi obblighi di gestione e controllo dei processi automatizzati. «Proprio per questo – sottolinea Vitulano – Barilla sta investendo molto in cybersecurity. Sull’altro piano della bilancia, digitalizzare significa anche avere a disposizione informazioni che non servono soltanto al business, ma al rispetto dei numerosi vincoli normativi di settore. Il fatto di poter monitorare la presenza di determinate sostanze e allergeni, permette di affrontare con ancora più tranquillità gli audit».
Quando a trasformarsi è un ambiente di lavoro tradizionale come l’officina delle biciclette – rileva Mauro Toso di Bianchi Bicycles – la difficoltà sta anche nella mancanza di un termine di paragone. «Per capire meglio i potenziali obiettivi, abbiamo adottato la strategia del digital twin, realizzando un modello virtuale della fabbrica. Attraverso opportune simulazioni abbiamo studiato le sequenze di produzione, per individuare eventuali colli di bottiglia». La conversazione si sposta inevitabilmente verso ciò che appare essere la preoccupazione più diffusa: la relazione tra il “prima” e il “dopo”, e la coesistenza dell’uomo con la macchina e con l’informazione digitalizzata, che è molto più strutturata rispetto alla conoscenza istintiva, talvolta connessa all’estro artistico, che risiede nelle menti e nelle mani degli operai. La trasformazione digitale ha il suo punto di partenza nella fabbrica, ma impone alla fabbrica modelli e procedure che le persone faticano ad acquisire. Simulando il futuro della sua fabbrica, Bianchi è riuscita a validare un approccio che ha letteralmente capovolto le modalità del passato. «Prima erano le persone a muoversi intorno alla bicicletta» – spiega Toso. Nel nuovo impianto, è la bicicletta che si sposta con tutti i pezzi e gli attrezzi necessari. Una vera rivoluzione che ha richiesto uno notevole sforzo di adattamento».
DIGITAL SKILL E SAPER FARE
Chi opera nella nuova fabbrica Bianchi deve affiancare competenze digitali che un tempo non erano necessarie. Al tempo stesso, se formare queste nuove competenze è necessario, non bisogna certo abbassare la guardia sulle competenze specifiche di un mestiere – l’assemblatore di biciclette – che le scuole professionali sembrano aver dimenticato (uno dei tanti effetti collaterali dell’automazione). Questo è un aspetto che alla Bianchi interessa molto. Al punto da prevedere opportuni momenti di formazione che non riguardano il software, ma pedali, freni e manubri. La ricerca del giusto equilibrio tra skill digitali e professionalità rappresenta una necessità condivisa da numerose aziende del settore manifatturiero. «Ogni accesso al nostro sistema di gestione della produzione – afferma Bresciano di Artsana – avviene in modo filtrato. I badge degli operatori includono le informazioni sulla formazione ricevuta, oltre ai livelli di idoneità sanitaria. Se non ho le necessarie competenze per utilizzare un impianto, non posso neppure accedervi». Tutte le aziende – secondo Gianpaolo Vitulano di Barilla – devono impegnarsi nella ricerca di questo equilibrio. «Nel mondo – osserva il responsabile delle architetture dati in Barilla – una grande percentuale di persone costituisce la cosiddetta manodopera. C’è un mix tra tradizione e tecnologie che deve ancora assestarsi e probabilmente porterà a una evoluzione qualitativa del lavoro umano». Il mondo della scuola deve e dovrà affrontare, sempre più attentamente, la dimensione dell’apprendimento in modo diverso, la stessa Barilla è impegnata con attività di digital academy che affiancano e, in qualche caso sostituiscono anche, quelli che un tempo erano corsi di formazione dedicati.
Giorgio Dossena di Qlik è convinto che l’automazione debba servire soprattutto a sgravare il lavoro delle sue parti più noiose e ripetitive, lasciando alle persone il tempo di pensare ad altro. «L’intelligenza artificiale generativa si prenderà carico di molte attività a basso valore aggiunto. Nell’ambito del data management, la sua funzione principale è quella di fornire un supporto per comprendere i dati in modo più approfondito. A titolo di esempio, Qlik ha integrato strumenti di intelligenza artificiale che guidano gli utenti delle nostre soluzioni attraverso l’interazione in linguaggio naturale. La vera sfida consiste nell’adattare questi strumenti a tutti i contesti lavorativi, mantenendo sempre l’approccio che li vede come tecnologie di supporto e non di sostituzione».
Secondo il responsabile IT di Pellini Fabio Pericotti, la formazione interna continua è l’unica possibile risposta alla necessità di ricostruire il rapporto tra uomo e macchina in questo momento di passaggio dalla rivoluzione industriale a quella digitale. «Ovviamente, questo può scontrarsi, soprattutto in realtà di medie dimensioni, con l’esigenza di continuità operativa: è complicato togliere, anche solo momentaneamente, risorse alla fabbrica per metterle a sedere in aula. Ma è l’unica strada da seguire per fare in modo che la manodopera diventi testadopera».
UNIFICARE LE PIATTAFORME
Insieme a tutte queste problematiche interne, l’industrial director di Artsana intercetta una sfida “esterna” alla fabbrica intelligente e data-driven. «I nostri prodotti sono destinati alle famiglie – spiega Roberto Bresciano – e rientra nella nostra missione accompagnarle nella scelta e nell’uso dei prodotti più adatti. Potrebbe sembrare un compito semplice, ma oggi persino questa decisione si è spostata nel mondo digitale, con le famiglie che prendono decisioni su Internet e sui social media». In aggiunta ai dati che scorrono attraverso le piattaforme gestionali e i sistemi di fabbrica, l’azienda manifatturiera digitale deve essere in grado di raccogliere e organizzare una vasta quantità di informazioni che circolano in modo caotico su questi canali. Secondo Pier Giuseppe Dal Farra di Orange Business, il ruolo fondamentale del system integrator consiste nell’agevolare connessioni e nell’offrire risposte mirate alle esigenze condivise, ma affrontate in contesti specifici. Le riflessioni sulle questioni di sicurezza ambientale e di controllo qualità conducono la discussione sulle attività svolte da Orange Business nel settore farmaceutico. «In questo contesto, la tecnologia Computer Vision assume un ruolo cruciale, facilitando il controllo del grado di purezza di una sostanza» – spiega Dal Farra. «Analogamente, nello scenario dei grandi cantieri, la stessa tecnologia può essere utilizzata per monitorare l’utilizzo dei dispositivi di protezione individuale». Le opportunità offerte da queste tecnologie e dalle applicazioni sono svariate, e per Orange Business, l’approccio più gratificante consiste nell’affrontare i progetti in modo collaborativo. L’azienda, grazie a progetti mirati di co-innovazione, da un lato sviluppa le soluzioni richieste dai clienti e dall’altro accresce il proprio know-how specifico su tematiche di particolare avanguardia. La risoluzione dei problemi richiede una comprensione approfondita delle relazioni e delle interconnessioni tra le variabili coinvolte. Dal punto di vista informatico, l’utilizzo isolato di piattaforme gestionali specifiche, come ERP, MES, CRM, CSM o canali social non è più adeguato alle esigenze aziendali moderne. «Nel complesso – conclude Dal Farra – l’approccio strategico richiede l’adozione di una piattaforma consolidata, una sorta di super piattaforma o piattaforma delle piattaforme, in grado di centralizzare, orchestrare e valorizzare l’insieme dei dati provenienti da queste fonti eterogenee, creando così un ecosistema sinergico che ottimizza l’intera gamma di dati aziendali».
Foto di Gabriele Sandrini
Point of view
Intervista a Pier Giuseppe Dal Farra, smart industries business expert di Orange Business: Il partner per l’Industrial DataOps
Intervista a Giorgio Dossena, presales manager di Qlik: Tutte le informazioni per decidere