La duplice sfida della crescita e della sostenibilità nella governance della smart factory. Dal cloud all’Edge, l’integrazione di AI e IoT trasforma la produzione, migliorando l’efficienza e riducendo gli impatti negativi. Sicurezza avanzata e standard interoperabili per una convergenza senza confini tra IT, OT e Business. Con la partecipazione di Bianchi Bicycles, Citterio, Corcym, Gruppo Montenegro, Marelli Automotive Lighting, Orange Business e Sopra Steria
Nell’incontro dedicato al tema della smart industry, l’obiettivo è dare spazio alle ultime tendenze della trasformazione dei processi produttivi all’insegna della digitalizzazione. Un traguardo che anche in un contesto di grandi complessità e difficoltà che toccano l’intera supply chain consente di vedere la fabbrica intelligente e data-driven come un potente fattore di “inversione di rotta” e crescita. Data Manager ha riunito intorno al tavolo alcuni dei principali protagonisti di questa rivoluzione: Bianchi Bicycles, Citterio, Corcym, Gruppo Montenegro, Marelli Automotive Lighting, Orange Business e Sopra Steria. Ai relatori è stato chiesto di analizzare lo sviluppo di tecnologie come il cloud – in particolare sul cosiddetto “Edge” il luogo della potenza di calcolo decentralizzata che sempre più spesso esigenze di tempo e riservatezza inducono a dedicare all’analisi Big Data “off cloud” – l’industrial IoT, la connettività wireless (5G, SD-WAN), l’uso di digital twin, l’ammodernamento dei MES, i sistemi di virtual e augmented reality applicati ai processi di fabbrica (controllo, prevenzione, manutenzione) e così via.
Oggi, la vera sfida di fronte alla quale ci troviamo tutti si chiama tuttavia sostenibilità, transizione energetica, lotta al cambiamento climatico. Considerando che un quinto delle emissioni di CO2 sono legate alla produzione industriale, essere sostenibili oggi non vuol solo dire ridurre l’impatto sull’ambiente attraverso bassi livelli di emissione e minor consumo energetico, ma anche ottenere significativi aumenti di efficienza, produttività, marginalità, qualità della vita dei lavoratori e dei responsabili della fabbrica. E in molti casi, ricevere un boost reputazionale che rafforza il brand aziendale, fidelizza i clienti e apre verso nuovi mercati. Tutti questi traguardi oggi sono raggiungibili anche attraverso la trasformazione digitale.
Attraverso una formula ormai consueta, la prima parte della tavola rotonda si focalizza sulle soluzioni tecnologiche adottate attualmente per trasformare l’ambiente produttivo e realizzare le singole strategie di sostenibilità. Ancora una volta abbiamo chiesto al panel di tecnici riuniti intorno al tavolo di non soffermarsi sulle questioni puramente tecnologiche ma di approfondire anche le modalità di attuazione e di governance, di azione sul piano organizzativo, dell’acquisizione e reskilling di nuove competenze, della gestione del cambiamento che le tecnologie determinano non solo nei processi, ma anche nei ritmi, nelle tipologie e nella cultura del lavoro.
LA SFIDA DELLA SMART FACTORY
Se la digitalizzazione deve sempre affrontare ostacoli che non sono solo di natura squisitamente tecnica, la seconda parte della tavola affronta le sfide – spesso inedite in sistemi di produzione immaginati nelle precedenti fasi dell’automazione – che la fabbrica digitale e interconnessa pone sul piano della sicurezza, dell’integrità del dato e della tutela della proprietà intellettuale. Un altro aspetto problematico, nel contesto manifatturiero, è il rispetto di un complicato sistema di regole che oggi tra l’altro supera i confini nazionali. Gli interlocutori al tavolo, hanno a lungo discusso anche su tutte queste zone di possibile attrito nei confronti di una trasformazione che le fabbriche continuano a cercare attivamente.
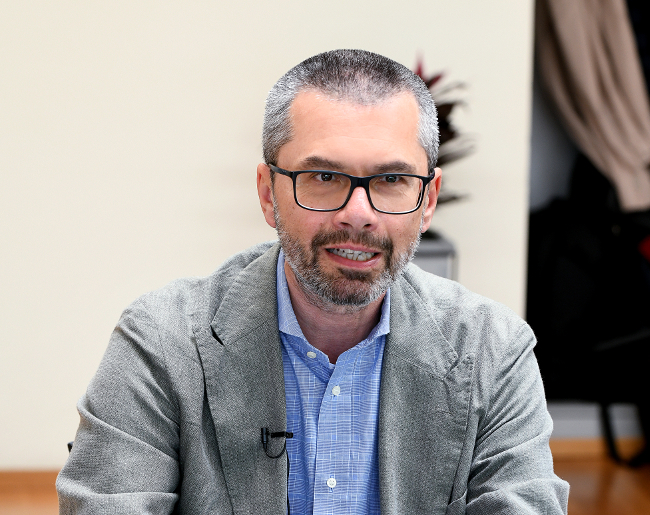
Ne è emerso il quadro di un settore produttivo effettivamente molto attento alle istanze dell’evoluzione tecnologica. Un’evoluzione che davvero consente, se ben implementata di ottenere significativi risultati in termini di ottimizzazione e una diversa capacità decisionale, basata su dati effettivi e per questo centrata su una collaborazione sempre più stretta tra business e responsabili dei sistemi informativi. Dalla conversazione tuttavia emerge che c’è ancora un inatteso nodo da sciogliere, quello riguardante una convergenza tra Information e Operation Technologies, ossia tra due diversi stili di considerare l’informatica e l’automazione. Sistemi di fabbrica e sistemi IT oggi dialogano certamente in modo più fluido, ma al di là di quelle che possono essere le inevitabili differenze, sembra esserci ancora parecchia strada da fare, nel comparto OT, a livello di una sufficiente adozione di standard che aiuterebbero le scelte trasformative delle aziende. E in questo possono avere un ruolo importante coloro che progettano, costruiscono e commercializzano i macchinari industriali di nuova generazione. Il ritorno di Stefano Faccio alla tavola dedicata alla fabbrica smart offre al relatore lo spunto per accompagnare il racconto delle sue opinioni professionali con una breve presentazione di un recente position paper pubblicato a maggio in occasione dell’ultimo SPS di Parma, l’importante fiera dell’automazione industriale che annovera il nome dell’head of Machinery Safety – Industry 4.0 & Digital di Manufacturing Marelli Automotive Lighting nel suo Comitato scientifico. Un comitato che vanta 150 esperti in rappresentanza di aziende manifatturiere, costruttori di macchine industriali e personaggi del mondo accademico.
GUIDA ALLA DIGITALIZZAZIONE
«Lo studio – spiega Faccio – segue la prima versione del paper apparsa lo scorso anno: una iniziativa di SPS per aiutare i decision maker che nelle loro realtà vogliono affrontare un percorso di trasformazione digitale. Anche in questa seconda edizione, molto più corposa e dettagliata, abbiamo voluto condensare le esperienze dei componenti del comitato in un documento che possa fungere da guida e riferimento». Il leitmotiv di questa nuova edizione, intitolata proprio “Linee guida per una trasformazione digitale umano-centrica nell’era dell’Intelligenza Artificiale” (già disponibile, insieme a un secondo capitolo uscito nell’estate, sul sito Web della manifestazione organizzata da Messe Frankfurt) si riferisce alla necessità di supportare l’adozione dei moderni sistemi di automazione con progetti di lungo termine, che abbiano al centro la collaborazione uomo-macchina, oggi rappresentata dall’intero corpus di ricerche, metodi e applicazioni dell’Intelligenza artificiale.
«L’Industria 4.0 che era stata immaginata in Germania tanti anni fa era puramente tecnologica, un’aggiunta che avrebbe fatto crescere le aziende di per sé» – afferma Faccio. «Solo dopo ci siamo accorti che tra automazione e trasformazione c’è l’uomo nel mezzo». Gli autori del position paper sostengono il ruolo fondamentale dell’AI e hanno voluto corredare il loro testo con i risultati di un questionario pensato per tastare il polso in materia di conoscenza, adozione e fiducia nei confronti di strumenti che – sostiene Faccio – possono portare le aziende manifatturiere verso un futuro popolato da robot collaborativi, principi di sicurezza fissati nella nuova direttiva uomo-macchina e criteri di sostenibilità come parte importante – dice il responsabile dell’innovazione in Marelli Automotive Lighting – della “trasformazione umano-centrica”.
STRATEGIE DI CAMBIAMENTO
Faccio illustra ai colleghi relatori il contenuto del documento introduttivo, costituito da una prima parte di carattere generale che si concentra principalmente su aspetti di visione strategica, generazione del valore, stato dell’arte delle tecnologie e nuovi modelli di business (per esempio, servitizzazione e “platform thinking”) a cui le nuove forme di automazione possono dar vita.
La seconda parte è completamente dedicata alle architetture a supporto di sistemi e processi in cui, partendo dalla classica piramide dello standard internazionale ISA 95 per lo sviluppo di un’interfaccia automatizzata tra sistemi aziendali e sistemi di controllo, commenta le architetture che meglio si adattano a supportare le potenzialità associate alle nuove tecnologie. il documento SPS cita per esempio framework come RAMI 4.0, ISO IoT, Web of Things, Industrial Internet Reference Architecture (IIRA), prendendone brevemente in esame vantaggi e svantaggi a seconda dei diversi ambiti di utilizzo. La terza parte affronta le tematiche di automazione avanzata e robotica, cybersecurity, il nuovo Regolamento Macchine e sicurezza anche informatica, alcuni recenti regolamenti europei (Digital Act, AI Act) e infine il passaggio dall’industry 4.0 a al 5.0, con le relative ricadute sul piano umano-sociale e ambientale. Oltre a rappresentare un’efficace introduzione ai capitoli che il comitato scientifico di SPS ha già pubblicato e sta preparando, il documento diventa dunque una sorta di compendio degli argomenti in discussione nel corso della tavola rotonda.
Tornando a indossare i panni del responsabile Industry 4.0 di Marelli Automotive Lighting, Stefano Faccio si sofferma infine proprio sulla questione AI, per parlare delle ultime novità che caratterizzano la sperimentazione dell’azienda sul fronte dei nuovi strumenti generativi. «Abbiamo lanciato una serie di proof of concept che hanno raccolto una grande adesione. Partiti da GPT3, oggi abbiamo attivato una istanza interna di GPT4 Turbo, con una serie di test che investono tutti i comparti aziendali, dalle risorse umane agli uffici acquisti e vendite, fino all’R&D e alla produzione cercando di sfruttare ogni possibile leva, a partire da un impegno sul fronte dell’edge computing che a mio parere è il modello implementativo più efficiente. I tempi – conclude Faccio – non sono particolarmente favorevoli agli investimenti in digitalizzazione, ma disporre di una visione complessiva, decidere in anticipo le aree da aggredire dà sicuramente modo di essere più efficaci. Ma la visione non basta. Come viene sottolineato nel position paper, implementare una tecnologia non è sufficiente se prima non si è passati attraverso una fase di revisione e ottimizzazione dei processi. Prima dell’adozione dev’esserci l’efficientamento».
ASSISTENTI CHATBOT
Tra gli use case che Marelli Automotive Lighting sta portando avanti in materia di GenAI, vengono citati il problema del troubleshooting che serve a risalire alle cause di un guasto o di un malfunzionamento di una linea. Perché non farsi aiutare da un chatbot che viene costantemente alimentato con dati operativi per risalire all’origine di un fermo macchina o di un problema di qualità? «In questo tipo di sperimentazione – spiega Stefano Faccio – il nostro non è un caso isolato: ho visto tanti analoghi esempi applicativi». Un altro campo d’azione è il già citato ambito della documentazione tecnica, dove i Large language model possono dare una grossa mano nel sintetizzare e correlare grandi volumi di complicati manuali di istruzione, linee guida e liste di specifiche.
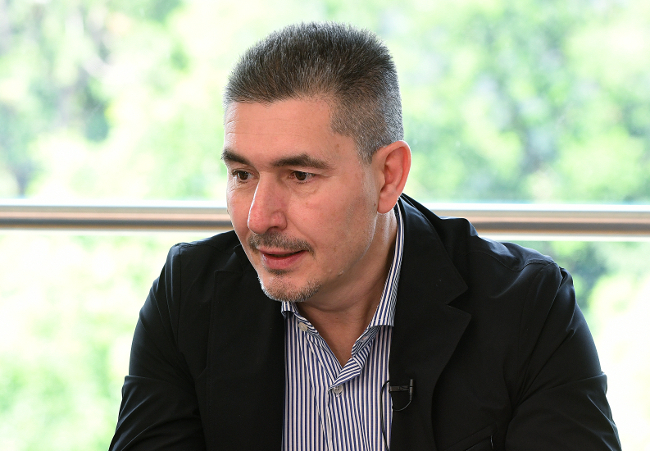
La fase preliminare di pianificazione auspicata da Faccio ha di fatto caratterizzato l’intera strategia di trasformazione digitale di Bianchi nello stabilimento di Treviglio. «L’impianto è stato riprogettato da zero per una ricostruzione che, avviata nel 2022 è stata ultimata in tempi record l’anno successivo» – racconta il CIO di Bianchi Bicycles Mauro Toso. «Abbiamo eliminato la classica idea di nutrire la produzione sul posto, creando viceversa delle slitte sospese su cui vengono trasportate le biciclette da assemblare e tutti gli elementi necessari. Questo ha comportato una rivoluzione di tutta la catena delle forniture. E la prima sfida è stata sfruttare il digitale proprio per capire se questo progetto poteva funzionare». Con i suoi collaboratori, Toso ha realizzato un dettagliato gemello digitale del nuovo lay-out. Una fabbrica simulata dove i responsabili dello stabilimento hanno potuto studiare i possibili colli di bottiglia, tenendo conto di due fattori. Da un lato un tipo di produzione ancora molto artigianale, dove la manualità prevale completamente sulla robotizzazione. Dall’altro la necessità di abilitare, per ciascun punto di sosta delle slitte, l’assemblaggio di due famiglie di prodotto molto diverse tra loro, la tradizionale bicicletta a spinta “muscolare” e i nuovi modelli elettrici a pedalata assistita. «Al contorno – prosegue Toso – c’è tutto lo stabilimento, nato fin da subito per essere sostenibile, in grado di autoalimentarsi nell’intero arco dell’anno e dotato di sistemi di condizionamento dell’aria che sfrutta le acque del sottosuolo e la rigenerazione».
L’ASSEMBLAGGIO 5.0
La nuova fabbrica di Bianchi nasce già in chiave 5.0, applicando concetti di ergonomia del lavoro e di preparazione dei kit di assemblaggio che riflettono – osserva il CIO – una mentalità molto «automotive», ancora estranea alla cultura dell’officina delle biciclette. «Oggi, le slitte si muovono lungo due chilometri di binari in uno spazio coperto di ottomila metri quadri dentro a un’area industriale che vale il doppio di questa superficie» – spiega Toso. «Tutto è governato dalla sensoristica IOT orchestrata da un sistema MES dedicato a ogni lavorazione che ha comportato anche un notevole sforzo a livello di reskilling delle persone. Una parte del personale ha preso parte ad attività di Academy interna, partecipando fattivamente allo studio della cosiddetta “bilancella”, la slitta che accoglie il telaio, le ruote delle bici e tutti i componenti e gli attrezzi necessari. Abbiamo studiato di sana pianta anche il packaging finale». In questo progetto, Toso ha avuto la fortuna di collaborare con una affiatata squadra interna (IT/Produzione/Logistica) e da una serie di specialisti di settore esterni, ma il successo della realizzazione è dovuto in prima battuta al coinvolgimento del management dell’azienda, che ha sponsorizzato, motivato e supportato il progetto.
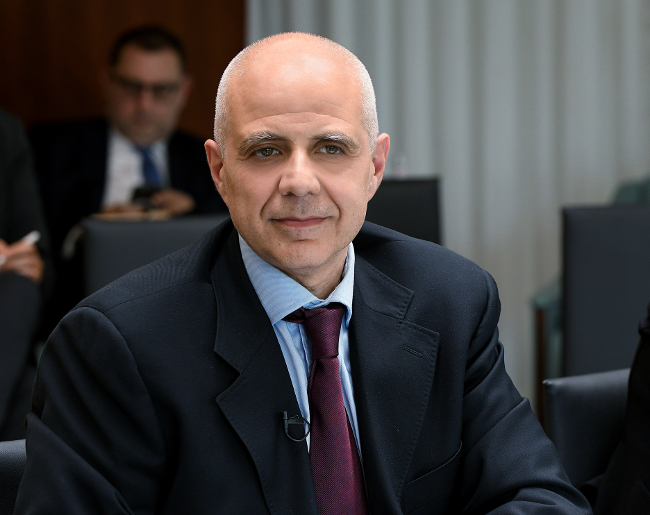
Gli argomenti esposti sin qui – dalla necessità di puntare a una tecnologia umano-centrica al costante fabbisogno di competenze e adattamenti di natura culturale – sono in linea con le esperienze dei clienti di un Tech Leader europeo come Sopra Steria. Nel suo intervento, Federico Chieppa, AI & Data offering lead di Sopra Steria Italia, spiega come le tematiche affrontate nei progetti che Sopra Steria è chiamata a supportare indicano come per una trasformazione che non sia solo fine a sé stessa il primo obiettivo sia quello di individuare i driver di business e il pieno coinvolgimento dei decisori. Il caso di Bianchi Bicycles dimostra che quando è possibile scegliere da zero un percorso nuovo si può fare una scelta di eccellenza. La vera sfida è quando la trasformazione deve innestarsi in una realtà consolidata, che non può permettersi di immaginare pause e avvicendamenti. «È qui – sottolinea l’esperto – che la tecnologia avanzata può solo in parte essere considerata un fine. È sempre lecita, insomma, l’ambizione di introdurre un ammodernamento, un nuovo strumento, ma questo deve sempre essere considerato soprattutto un mezzo». Anche nel campo applicativo dei dati, caratterizzato oggi dalla presenza di algoritmi di machine learning, nella transizione tra presente e futuro, bisogna sempre saper creare i presupposti per facilitare il cambiamento. «Inutile, per esempio, introdurre strumenti di AI generativa se coloro che devono fruirne hanno un gap di competenza che impedisce di formulare ai chatbot le domande corrette».
VOGLIA DI LEAN MANUFACTURING
In questo momento, sulle tecnologie di frontiera che rappresentano il tema di fondo di questa discussione, le grandi organizzazioni possono far leva sulle loro maggiori capacità di integrazione end to end. «Per esperienza vedo che nelle realtà più piccole, anche quando è facile immaginare dei proof of concept, manca poi la capacità di scalare, c’è troppa separazione tra IT e OT cosa che rende impossibile quel mantra della convergenza che anche il documento di cui ci parlava Stefano Faccio identifica come centrale» – prosegue Chieppa di Sopra Steria.
«Eppure c’è davvero appetito nei confronti di applicazioni e modalità che le aziende vogliono acquisire per snellire i loro processi e ridurre i costi che incidono sulle marginalità. Un’altra grossa aspettativa è l’efficienza e la manutenzione degli impianti in ottica predittiva, quella resa possibile da una approfondita analisi dei dati storici coadiuvata dagli algoritmi di AI. È la ragione per cui è fondamentale avvicinarsi al dato con una strategia adeguata a garantire la qualità e l’accessibilità dei dati». L’esempio fornito da Enrico Clerici, digital transformation director di Gruppo Montenegro va esattamente nelle direzioni appena indicate. «Oggi anche un prodotto rimasto fedele alle ricette originali di fine Ottocento deve sapersi rinnovare in termini di produzione e sostenibilità» – afferma Clerici. «Per competere dobbiamo essere sempre più efficienti e in questo senso la digitalizzazione è un’arma fondamentale sia in termini di miglioramento del processo produttivo sia di innovazione del prodotto». Gruppo Montenegro ha avviato il suo percorso di trasformazione digitale perfettamente conscia del fatto che un viaggio come questo può avere solo un punto di partenza e non di arrivo. «L’idea virtuosa che ci ha sempre sostenuti – tanto nella parte operations che nell’IT nella scelta delle applicazioni commerciali e consumer oriented – è la necessità di partire dall’organizzazione, dalle competenze interne, gli stili di lavoro. L’elemento umano è centrale perché non siamo semplici “utilizzatori”: le persone devono guidare le attività di trasformazione perché quest’ultima alza l’asticella per tutti. Tuttavia, non sono sufficienti i corsi di formazione per riuscire a far proprio un cambiamento così radicale e poter contribuire alla realizzazione di un progetto».
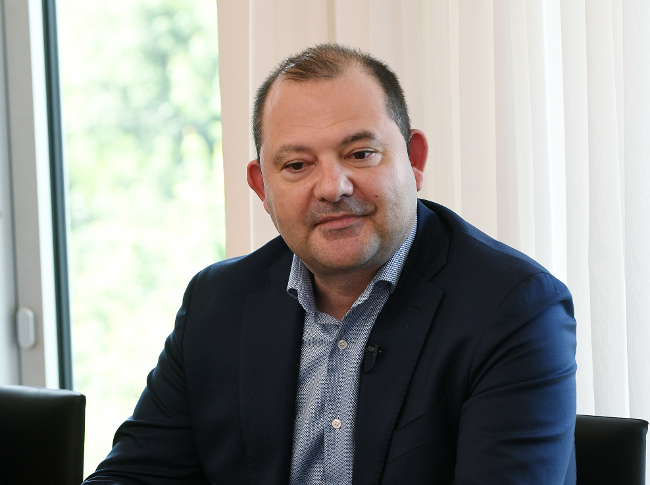
La digitalizzazione di Montenegro inizia nel 2019 con una accurata fase di valutazione e ha coinvolto dapprima l’aspetto organizzativo. «Abbiamo identificato diverse aree di intervento, per esempio il demand planning, con l’obiettivo di migliorare la capacità di definire la richiesta e la movimentazione dei materiali. In seguito, si è passati al training della forza vendita, in particolare rivolta all’export, con l’obiettivo di identificare le informazioni che avrebbero potuto migliorare il lavoro sul campo e dare maggior valore agli stessi clienti. In parallelo è andata avanti l’adozione di una piattaforma PLM per la gestione dei prodotti. In meno di un anno, siamo riusciti a realizzare un sistema che ci consente di ottenere le informazioni che servono all’analisi e all’individuazione dei colli di bottiglia».
Nel futuro, Clerici si aspetta enormi benefici nelle strategie di go-to-market di un gruppo che tra l’altro ha diversificato molto la sua produzione, muovendosi dal comparto degli alcoolici verso segmenti food con brand come Bonomelli, Cannamela, Cuore e altri. Anche in Montenegro non manca né l’interesse nei confronti del dato e della sua qualità, né la curiosità nei confronti della GenAI. «Ci interessiamo anche ai nuovi strumenti dell’intelligenza artificiale e, come tutti credo, sviluppiamo piccoli progetti con i chatbot generativi» – spiega Clerici. «A mio parere sarà un elemento dirompente, in grado di dare enormi benefici ma non si può pensare di applicarlo come una bacchetta magica: dovremo lavorare sempre di più sulle strategie. Siamo partiti da un programma di formazione rivolto a un gruppo di persone che rivestiranno il ruolo di “AI Angels” e daranno una mano al nostro dipartimento di innovazione digitale, focalizzando meglio finanziamenti e aree di sperimentazione dei proof of concept».
SE IL PRODOTTO TI SALVA LA VITA
Le imprese possono essere di dimensioni relativamente piccole in termini di collaboratori, stabilimenti e volumi di produzione, ma se il prodotto è un po’ più complesso del solito, l’intervento della digitalizzazione diventa letteralmente vitale. Come nel caso di Corcym, un’azienda indipendente nata da un’operazione di carve-out del gruppo italo-americano Sorin (in seguito, LivaNova) a sua volta erede di una tradizione industriale che risale agli anni 50 del secolo scorso, quando Fiat e Montecatini, ancora prima che questa diventasse Montedison, costituirono una joint-venture per trovare applicazioni industriali alla nascente ingegneria nucleare civile. Sorin si convertì in seguito alla produzione elettromedicale e biomedica. La nuova realtà è stata creata intorno all’esclusiva linea prodotti di Corcym: le valvole cardiache.
«Com’è facile immaginare è una produzione soggetta a innumerevoli controlli» – spiega il CIO Saverio Nucci. «Ogni prodotto viene serializzato in lotti e ogni tool impiegato deve essere certificato per una specifica fase produttiva. Compresi i lavoratori stessi, tutto deve essere puntualmente tracciato dall’inizio alla fine. Disporre di una piattaforma MES è centrale per l’efficienza dello stabilimento e deve disporre di funzionalità che servono a rendere le informazioni di tracciamento disponibili in caso di controllo». Nell’ambito biomedico una valvola cardiaca artificiale appartiene alla Classe III, quella che individua a livello mondiale i dispositivi impiantabili che vengono a diretto contatto con gli organi e il sangue umani. Dal loro corretto funzionamento dipende la vita dei pazienti. «Non è solo una questione di controlli successivi» – spiega Nucci. «Il sistema deve essere in grado di bloccare una produzione prima di poter sfornare un componente rischioso, per cui è necessario avere una latenza bassissima anche nel calcolo dei possibili fattori di rischio e la potenza di calcolo deve risiedere sulla linea».
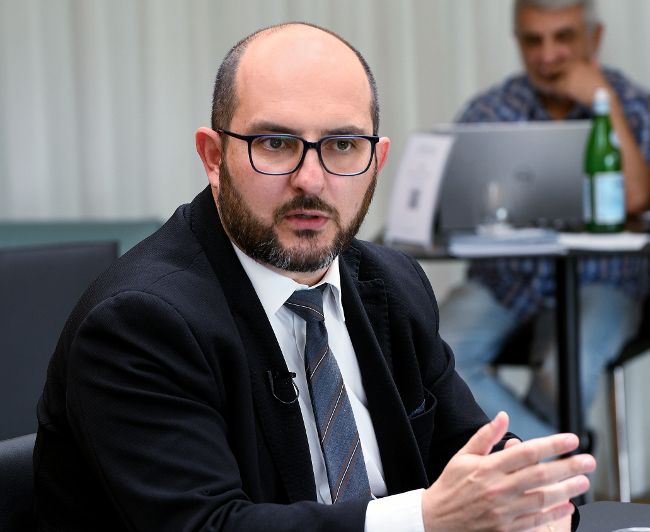
Come nel caso di Bianchi, e incoraggiata da una età anagrafica estremamente giovane (la fondazione di Corcym risale ad appena tre anni fa), l’azienda che in Italia ha i suoi impianti nel Vercellese ha sposato sin dall’inizio ogni possibile innovazione. Questo, tuttavia – precisa Nucci – non esclude la presenza di apparati legacy, spesso autoprogettati, che Corcym ha utilizzato in passato sotto l’insegna Sorin e che oggi devono poter dialogare con i sistemi informatici avanzati e aperti a tutte le possibili future evoluzioni. «Dentro a ogni valvola si possono contare un centinaio di passi costruttivi e questo – sottolinea Nucci – contribuisce a generare una mole davvero imponente di informazioni. Senza il machine learning e l’intelligenza artificiale non riusciremmo ad analizzare tutti questi dati».
In questa chiave, il MES adottato da Corcym e il team informatico guidato da Nucci avranno una funzione sempre più mirata all’obiettivo della sicurezza richiesto dal mercato e dai regolatori. «Il nostro compito è quello di riuscire a valorizzare al massimo i dati di cui disponiamo. Oggi, questi dati sono soprattutto orientati a alimentare i controlli e i test effettuati, ma se riuscissimo a correlarli meglio, con l’AI, sicuramente riusciremmo a intercettare errori e anomalie in tutte le fasi della produzione. Eliminare questi colli di bottiglia, visto il carico formativo e di impegno che pesa sulla risorsa umana, aiuterebbe rendere più veloce e produttiva la fabbrica, senza alcun rischio per i destinatari delle valvole, o addirittura incrementando la qualità complessiva. Oggi – conclude il CIO –tutte le iniziative di trasformazione digitale dell’IT, implementante in parallelo con la digitalizzazione lato operations, punta verso questa capacità».
DAI DATI ALL’EFFICIENTAMENTO
Intorno al tavolo della discussione il CIO di Corcym siede proprio di fronte a Paolo Fila, suo omologo di Citterio. «La prima affermazione che mi sento di sottoscrivere – riconosce Fila – ormai quasi al termine del primo giro di interventi, è che la trasformazione non può essere solo tecnologica. E questa è una delle ragioni per le quali in Citterio abbiamo cominciato a parlare di lean manufacturing, un concetto che nell’industria alimentare è arrivato in ritardo rispetto ad altri settori. Il punto è che prima ci sono le persone, la raccolta manuale del dato, l’esposizione dell’informazione alla fine della linea produttiva. Solo dopo interviene l’idea del miglioramento, della consapevolezza che la tecnologia ci aiuta dove noi possiamo interpretare dieci dati da una linea che ne genera mille».
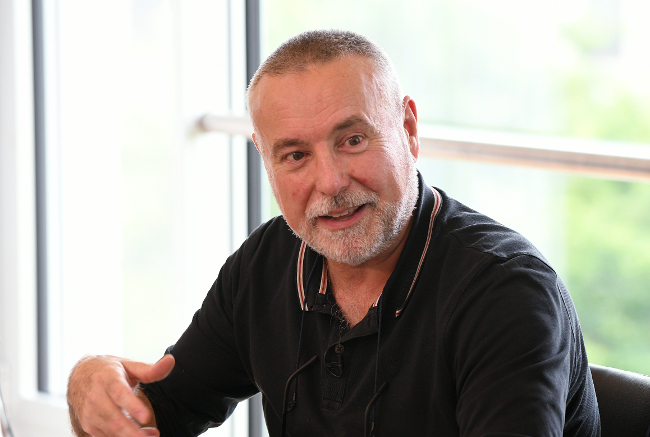
Come gli altri colleghi intervenuti prima di lui, Fila è chiamato ad affrontare la questione del valore del dato all’interno di sistemi di produzione che negli ultimi anni hanno dovuto risolvere il problema dell’integrazione e della comunicazione di impianti estremamente variegati. Attraverso l’adozione di standard e protocolli che non sempre rendono così fluido e immediato il dialogo. In Citterio, il livello di complessità è notevole se si pensa che Fila è responsabile della digitalizzazione di otto stabilimenti per un totale di 45 linee. Come si affronta questa complessità? «Il percorso tracciato è quello che abbiamo descritto finora. Si parte dal ruolo delle persone, dell’importanza della loro partecipazione al cambiamento e si comincia a raccogliere in modo organico una grande massa di dati che gli algoritmi di machine learning di aiuteranno a interpretare. Citterio in questo momento è concentrata sulle linee di produzione con un approccio misto edge-cloud. Il MES è installato localmente nei nostri stabilimenti, ciascuna istanza dialoga localmente con le macchine di produzione. I dati raccolti vengono centralizzati in cloud su una piattaforma di business intelligence che man mano verrà arricchita con l’AI».
Centralità del fattore umano, integrazione IT/OT, intelligenza artificiale sono temi che Orange Business ha integrato sia nella propria offerta tecnologica sia nella sua attività consulenziale. «Siamo strutturati sulla base di una serie di proposte di valore, come la sicurezza e la connettività, e soprattutto, in seguito all’emergenza pandemica, su un nuovo modo di lavorare» – spiega Pier Giuseppe Dal Farra, smart industries business expert di Orange Business. Come si opera oggi in campi applicativi così intrecciati tra loro nel contesto sfidante della fabbrica digitale? «Ho sentito citare in diversi interventi situazioni che ho riscontrato in molti dei nostri clienti. L’esigenza di tracciabilità menzionata da Corcym mi ha ricordato il caso di un importante gruppo leader nella produzione di motori per aereo, che ha tratto grande beneficio dalle tecnologie come il digital twin. Nelle sue fabbriche, sono operativi circa 25mila strumenti diversi che si spostano all’interno degli spazi di produzione. Un sistema avanzato fornisce informazioni precise sul posizionamento e la configurazione di questi strumenti, facilitando notevolmente le decisioni riguardanti il riacquisto e la sostituzione. Questo rappresenta un eccellente esempio di utilizzo delle tecnologie digitali».
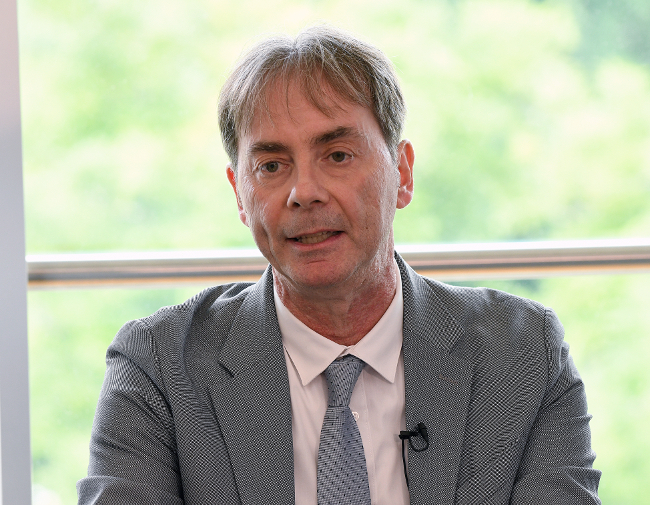
Parlando di tecnologia human-centric e di sostenibilità, Dal Farra sottolinea le ragioni fondamentali che oggi spingono tutte le imprese manifatturiere a muoversi in direzione di una maggiore sostenibilità ambientale. «Innanzitutto, c’è una ragione giuridica. Oggi, le varie legislazioni nazionali e sovranazionali con le loro normative sono il vero elefante dentro al negozio di cristalli: non rispettare certe regole può avere conseguenze molto serie. Un secondo punto, legato al bisogno di sostenibilità, nasce dalla necessità di rispondere, anche con i propri investimenti, alle richieste provenienti dalle nuove generazioni di lavoratori che pongono sullo stesso piano stipendio, carriera e attenzione all’ambiente. Infine, non dimentichiamo l’aspetto finanziario: un bilancio ambientale ed energetico in regola significa non solo poter accedere a finanziamenti e incentivi, ma essere anche più competitivi».
L’ambiente oggi è il filo conduttore che unisce molte applicazioni avanzate della tecnologia. In questo campo, Orange Business è convinta che il modo migliore per “insegnare” agli altri sia dare l’esempio. «Il nostro gruppo – spiega Dal Farra – è sulla strada del traguardo della piena neutralità carbonica entro il 2040. Utilizziamo al 50% solo fonti energetiche pulite, abbiamo ridotto del 30% le nostre emissioni. Da molto tempo, ogni consumabile viene tracciato per evitare sì che si disperda nell’ambiente e per essere il più possibile riciclato».
NUOVI MODELLI DI AUTOMAZIONE
Nella parte di discussione dedicata alle criticità che possono rallentare – quando addirittura non vanificare – un progetto di digitalizzazione della fabbrica, Stefano Faccio di Marelli Automotive Lighting mette sul tavolo il problema della cybersecurity che oggi si aggiunge a quello della sicurezza fisica (“safety”) di macchine e persone. Guardando all’esempio di Bianchi, in questo senso fortunata a implementare le sue strategie digitali nel greenfield – osserva Faccio – le vere difficoltà nascono nel cosiddetto brownfield, dove possono essere presenti diverse tipologie di macchine di diversi fornitori. «A dispetto di standard affermati come quelli proposti da OPC UA e altri consorzi, la protezione degli impianti legacy è molto complicata. Ma è un problema che il nuovo regolamento macchine in vigore a partire dal 2027 ci impone di affrontare».
Faccio vuole anche contestualizzare meglio i cambiamenti che riguardano framework come ISA 95 e RAMI, utilizzati come modello ispiratore di ogni progetto Industry 4.0. «Il famoso modello a piramide di ISA 95 è superato se prendiamo in considerazione anche le tecnologie dell’edge computing, su cui personalmente faccio molto affidamento come arma per superare i limiti computazionali dei processori PLC, normalmente utilizzati dagli impianti industriali, e aggiungere intelligenza alle nostre macchine. Le ultime tendenze architetturali inducono a passare da un modello piatto e bidimensionale a un concetto “tridimensionale” di ecosistema che ci porterà a superare le difficoltà operative della digitalizzazione. La priorità resta quella di definire una strategia concreta e di creare quello che io chiamo “allineamento dei pianeti”. Tutti, dall’amministratore delegato fino all’ultimo operatore devono credere nella trasformazione: se salta anche soltanto un anello della catena decisionale, il progetto rischia di andare in sofferenza».
A conferma dell’importanza di una pianificazione concepita dentro a un intero ecosistema, ci sono le parole del CIO del nuovo stabilimento Bianchi. «Forse, un approccio greenfield può facilitarti la vita, ma per noi i pilastri rimangono i processi interni alla fabbrica e le attività da implementare, come il “kitting”, l’equipaggiamento delle nostre slitte con a monte un magazzino parti che ti guida costantemente. Solo questo aspetto – rivela Mauro Toso – ha richiesto un anno di studi accurati, persino nel misurare al millimetro gli spazi di manovra all’interno della nuova officina». Anche quando ci si affida a un singolo committente per la realizzazione dell’impianto – osserva infine il CIO di Bianchi – si finisce per scontrarsi con le mille piccole idiosincrasie che caratterizzano le macchine industriali: un problema che la simulazione tramite digital twin e lo studio dei dati storici può aiutare a risolvere. Bianchi sta lavorando anche per migliorare il proprio sistema di pianificazione della produzione con strumenti dotati di maggiore intelligenza e autonomia nel prendere decisioni semplici senza coinvolgere per forza gli operatori. «Chi opera in fabbrica ha bisogno di tool sempre più trasparenti».
STRATI DI FRUIZIONE
Gli studi di valutazione e di benchmarking – riconosce Federico Chieppa, portando ancora una volta al tavolo l’esperienza accumulata da Sopra Steria nella sua azione di partner di tanti progetti di trasformazione – servono proprio a stabilire il grado di maturità che un’impresa ha raggiunto in previsione di un piano di upgrade tecnologico. Chieppa si sofferma sull’approccio utilizzato nelle modalità di implementazione di due clienti francesi di Sopra Steria Group: una grande impresa attiva nel campo della posa di cablaggi sottomarini e un’importante casa automobilistica, entrambe impegnate su ambiziosi progetti di edge computing.
«Nel primo caso – racconta Chieppa – si è trattato di un sistema distribuito, con potenza di calcolo distribuito e pesante impiego dei protocolli di comunicazione 5G, per il controllo della precisione della posa. L’obiettivo era di ottenere una forte autonomia delle varie applicazioni nelle situazioni terra, superficie del mare, profondità. Approccio opposto a quello adottato dal costruttore di auto, che ha centralizzato il benchmarking di decine di applicazioni da selezionare, implementandole poi in contemporanea in trenta stabilimenti diversi». Una volta realizzata l’infrastruttura di controllo e raccolta dei dati – prosegue l’esperto di Sopra Steria – le difficoltà principali di solito riguardano proprio l’aspetto della messa a valore dei dati. «Anche quando questi dati vengono raccolti in modo corretto – sottolinea Chieppa – non è detto che siano immediatamente fruibili». In molti casi, Sopra Steria è chiamata a intervenire proprio su quegli strati intermedi che consentono di “ammorbidire” i dati, raccolti da fonti diverse, in un semilavorato che possa essere dato in pasto agli algoritmi di business intelligence».
Enrico Clerici di Montenegro e Paolo Fila di Citterio concordano sul fatto che la mentalità data-driven sia ormai ampiamente accettata da tutti.Entrambi però pongono un problema di certificazione delle fonti. «Per anni, si è parlato di dati in senso astratto, mentre nelle fabbriche ci si accontentava di qualche report di base» – osserva il digital transformation officer di Montenegro. «Oggi, si fa decisamente sul serio e con le nuove tecnologie è relativamente semplice raccogliere dai nostri processi informazioni che un tempo sembravano fantascientifiche. Ci sono tanti aspetti che dobbiamo ancora dominare, a partire dalla cybersecurity, dove conta molto la capacità di gestire le informazioni distinguendo tra dati sbagliati e dati corretti. In futuro, credo che non esisterà solo chi genera i contenuti, ma anche chi li certifica».
CHI CERTIFICA L’INFORMAZIONE?
Un’opinione condivisa da Fila, che per la capacità produttiva e commerciale di Citterio immagina una evoluzione ricca di strumenti in grado di ottimizzare l’impiego e l’efficienza delle sue macchine e di realizzare un match sempre più perfetto tra capacità, reattività e qualità produttiva da un lato e gusti ed esigenze dei consumatori dall’altro. «A patto che venga affrontato il problema dell’attendibilità delle informazioni, non solo quelle che si possono acquisire e certificare all’interno, ma anche quelle pubblicamente disponibili su Internet. Personalmente – conclude Fila – ritengo che a un certo punto sarà necessario l’intervento di un regolatore».
Il problema della governance del dato sembra essere la preoccupazione principale anche in casa Corcym. «Più ci si sposta verso l’automazione e l’autonomia decisionale delle macchine, più diventa centrale il concetto di garbage in, garbage out» – afferma Saverio Nucci. Nell’implementare il suo MES, Corcym ha costituito creato un team di data management che costruisce i dati in modo centralizzato e li rende omogenei e coerenti rispetto a tutto l’ambiente produttivo. È ovvio che per gestire queste problematiche occorrono competenze di processo. «Se un data scientist non ha una visione completa del processo si rischiano risultati imprevedibili, specie con tecnologie tanto vivaci». Nucci conclude il suo intervento con un pronostico: «In questa crescente compenetrazione di ruoli e linguaggi tra tecnologia, produzione e business, in un futuro forse non lontano non esisteranno dipartimenti IT separati perché le funzioni saranno in qualche modo “embedded”, anche sul piano organizzativo».
In un intervento che funge da postfazione a una tavola rotonda animata e ricca di spunti, Pier Giuseppe Dal Farra di Orange Business evidenza la forte spinta del settore manifatturiero verso un livello ancora più elevato di automazione e “intelligenza” integrata. E riconosce che insieme ai prodotti, gli impianti generano anche dati, rendendo il tema della cybersecurity in fabbrica centrale. «Quando parliamo con clienti e partner la sicurezza è quasi sempre la questione principale». Per Orange Business, la cybersecurity non è un semplice “prodotto” o una “soluzione”, ma un processo fondamentale, strettamente legato al modo di operare all’interno di una organizzazione aziendale. Un processo all’insegna dell’approccio Zero Trust: «Niente può essere dato per scontato e ogni operazione deve essere monitorata e autorizzata».
SPAZI DI DIALOGO
Orange Business offre ai suoi clienti nel mondo migliaia di esperti in sicurezza con un piano di azione che parte da una fase di accurato assessment delle esigenze e delle vulnerabilità, per poi implementare rigorosi criteri di segregazione delle risorse e di continuo monitoraggio. Si occupa della protezione di ambienti estremamente complessi, come nel caso di un grande gruppo industriale che ha messo in sicurezza più di cinquemila access point wireless e l’intera infrastruttura di switch, riducendo al minimo (circa il 3%, secondo Dal Farra) l’impatto complessivo sul traffico della rete e curando anche aspetti come la simulazione degli attacchi e la formazione del personale. «Ho seguito con interesse i numerosi accenni alla valorizzazione dei dati e concordo sulla mancanza di una diffusa standardizzazione nel settore. Carenze che riguardano anche le piattaforme software citate, i MES, gli ERP, non solo i dispositivi e gli impianti» – afferma Dal Farra.
Orange Business propone un approccio basato sulla creazione di strati di comunicazione e omogeneizzazione attraverso il concetto di Unified Name Space (UNS). Questa architettura intermedia organizza e coordina le diverse fonti di dati dell’automazione industriale in uno spazio virtuale unificato. L’Operational Technology ha molto da apprendere dagli avanzamenti dell’Information Technology nel campo del middleware e dell’integrazione di oggetti, software e hardware eterogenei. Questi avanzamenti si basano sull’astrazione, il disaccoppiamento e l’emulazione, funzioni che spesso la semplice standardizzazione di interfacce, linguaggi e protocolli non riesce a garantire. La completa convergenza tra IT e OT permette alle aziende di superare le tradizionali barriere tra i silos tecnologici e funzionali, creando un ambiente più agile e reattivo alle sfide del mercato. L’impegno attuale verso questa integrazione promette di trasformare non solo le operazioni tecniche, ma anche il business nel suo complesso. Questo modello di convergenza non rappresenta solo un’opportunità per ottimizzare le operazioni aziendali, ma funge anche da catalizzatore per promuovere trasformazioni positive in settori cruciali della società contemporanea.
Foto di Gabriele Sandrini
Point of View
Intervista a Pier Giuseppe Dal Farra smart industries business expert di Orange Business: Governare l’eterogeneità
Intervista a Federico Chieppa AI & Data offering lead di Sopra Steria Italia: Intelligenza artificiale da domare
EOS Solutions: L’intelligenza artificiale nella Fabbrica del Futuro